Production
Services
What We Do
Zinc die casting
Aluminum die casting
Additive manufacturing
Plastic Extrusion
What We Do
Sheet metal
CNC Machining
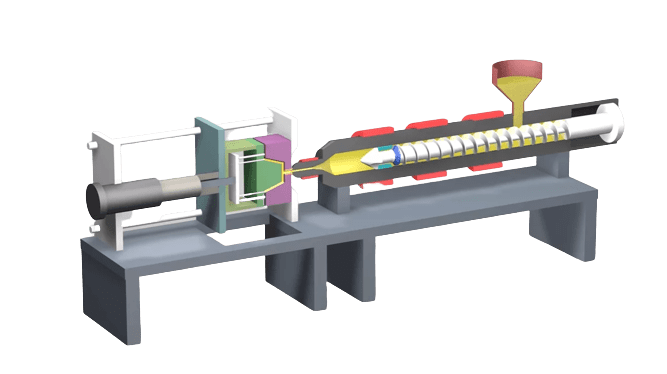
Injection Molding
Aluminum Extrusion
Get a Quote For Your Project
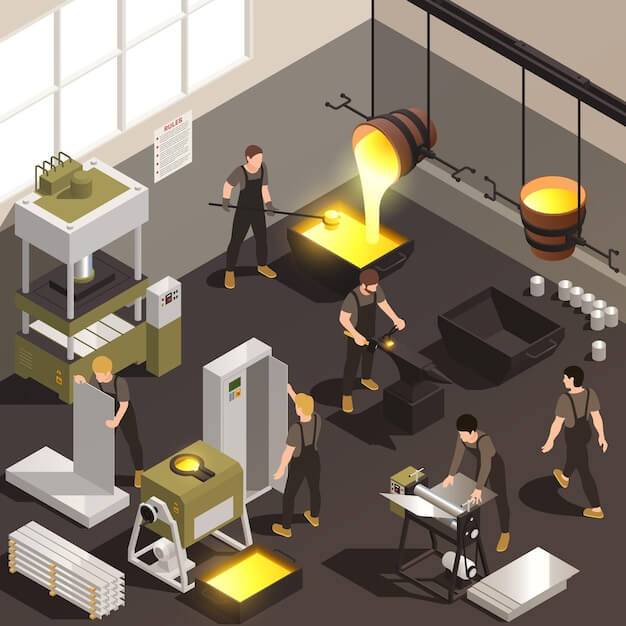
Zinc Die Casting
Zinc die casting is a metal casting process where molten zinc (often a zamak alloy) is forced into a mold cavity. The mold cavity is created using two hardened tool steel dies which have been machined into shape and work similarly to an injection mold during the process
HAWIDO offers outstanding zinc die casting services for high-quality components at a great piece part price. To achieve this, we are able to acquire raw zinc alloys at very low costs. (We don’t focus on any single alloy, either – we are proud to provide die casting for every commercially available zinc alloy on the market.) Due to this and our highly efficient manufacturing processes, we are able to offer a price per part that is 10 – 20% below our competitors.
For affordable zinc die casting services, we have focused on tooling prices, one of the larger costs involved in die casting. We are proud to offer tooling at extremely low prices, generally 10% of the costs of our competitors. Our low per-part costs and tooling costs make zinc die casting within reach of even the smallest manufacturers.
Zinc die casting services from HAWIDO will provide you with an accurately cast and economical product every time to meet your specific needs.
Zinc Casting Advantages
Zinc alloys used in die casting development possess properties that make production simple, while providing an end-product that is durable. Zinc’s strength and hardness administer high impact strength and stability that make assembly uncomplicated. The high ductility of zinc alloys is ideal for the die casting process with a strong ability to be contorted and expanded without fracturing under pressure. Other strengths of zinc alloys used in die casting are:
- Low cost raw material for one of the most cost-effective processes and end products possible
- Strong stability allows a long-lasting end product with high quality finishing properties
- Thin walls assist in corrosion resistance for end products, increasing ability to outlast harsh environments
- Zinc is one of the easiest alloys to cast: it offers high ductility, high impact strength, and is easily plated
- It is economical for small die cast parts
- Zinc has a low melting point
- It promotes long die life
Aluminum Die Casting
Aluminum die casting is a metal casting process through which forcing molten aluminum alloy under high pressure into a mould cavity. The basic operation of aluminium die casting is to fill a mold with liquid metal and press it into the designed geometry. Everything begins with the mold cavity, which is created using two steel dies that have been machined into shape. Aluminum alloy die casting is precision and reliable process that allows the metal to be cast and molded into the desired shapes in a safe way, which is widely applied in metal forming as the choice of most industrial projects requires metal components.
How Does Aluminum Die Casting Work?
The casting aluminum process applies a steel mold for the production of a large number of castings in rapid succession. The mould or die can be divided into two sections that mounted securely in the machine, one of them are moveable while another part is stationary. In the beginning, two die halves are clamped together tightly by the die casting machine. Then inject the molten aluminum into the mould cavity, where it hardens rapidly. After the aluminum alloy castings become solidified, separate from the mold halves, and the casting is ejected. The complexity of mold design is according to the desired aluminum casting parts, simple or complex metal castings can be made with Hawido aluminum casting service
Are you considering a cost-effective die casting project? Working with Hawido– a specialty aluminum die casting services supplier is the right choice. we are capable to assist our customers including engineers and designers to bring their aluminum die casting design to a real product that meets or exceeds their expectations, while maintaining the economy of the casting supplies at the same time. Advanced manufacturing equipment and measuring devices are fully equipped at our casting foundry to enable us to always supply high-quality aluminum die casting parts, zinc die casting parts, metal molds, and casts with competitive prices, innovative design, flexible service, quality assurance, and short delivery time. Our professional technicians and operators will seriously complete each step throughout the production and testing process, to ensure each aluminum die casting product functions normally and can last a long time.
Quality Control: We use a quality assurance checklist for all of our products to effectively track, examine, and verify whether the produced aluminum castings meet the necessary standards and requirements.
Broad Applications: Our precise aluminum casting parts and mouldings serve lots of critical industries and leading companies.
Plant and Facilities: We have engaged with a large aluminum casting factory with die casting manufacturing machinery and up-to-date measuring instruments.
OEM Capacity: If you need custom aluminum castings with specific configurations, our aluminum casting service can realize your complex designs.
High Productivity: reliable raw material supplies and a team of trained staff enable aluminum die casting parts to be manufactured with high efficiency within the promised period.
Low Cost: due to the aluminum is an economical metal casting option and our cost control on the process, our aluminum casting parts at lower prices than other aluminum castings manufacturers.
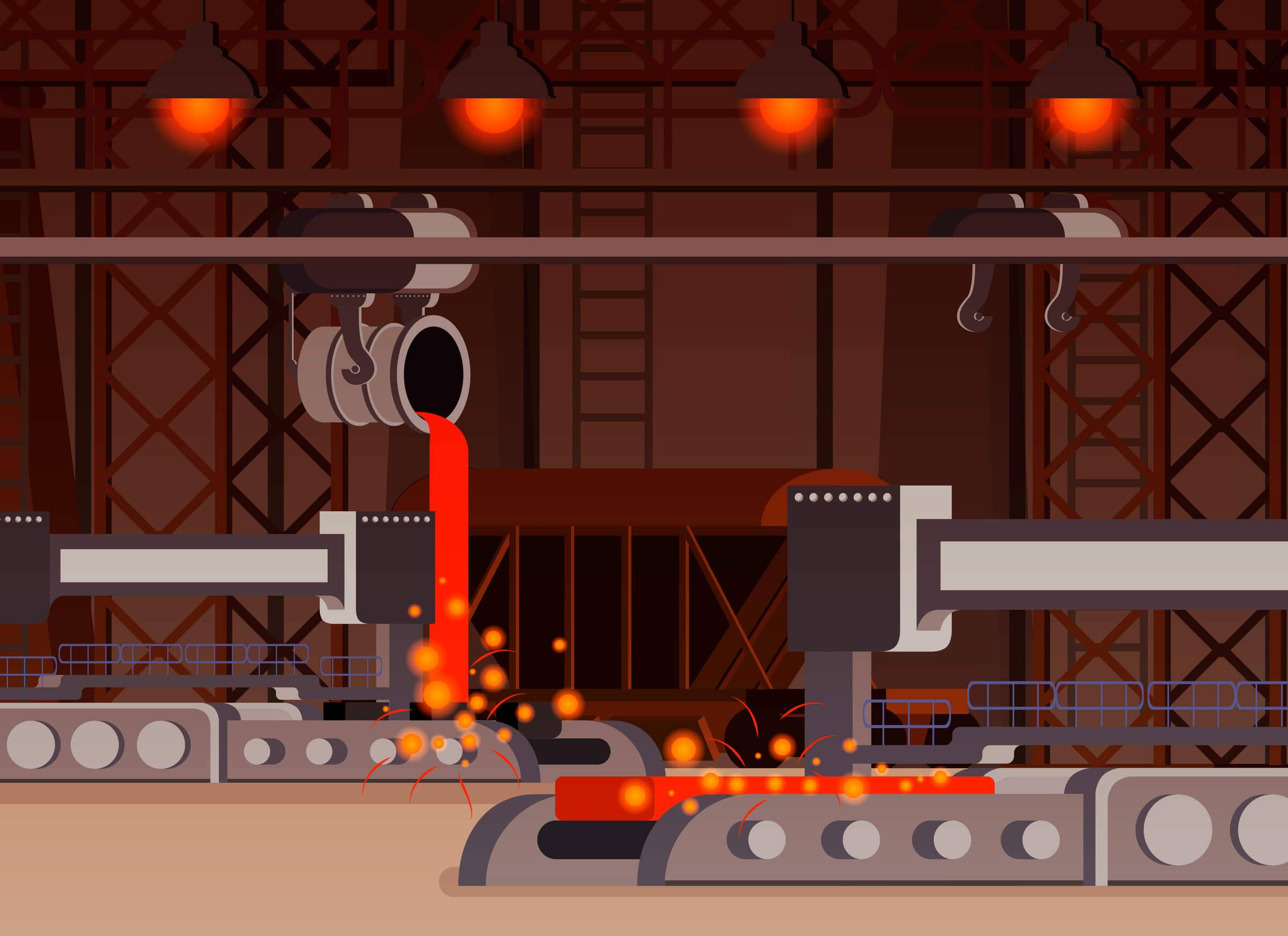
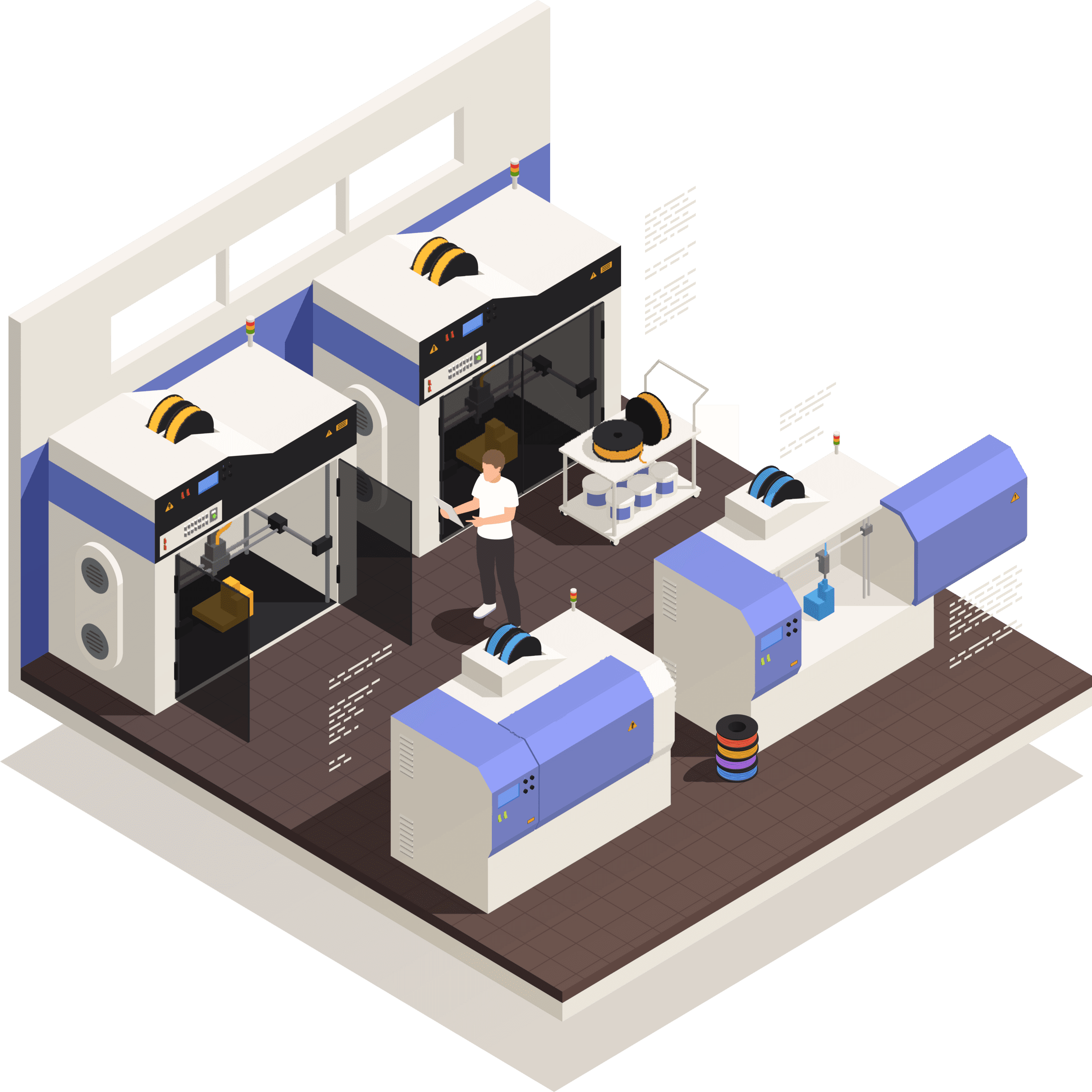
Additive Manufacturing
Additive manufacturing has gone through somewhat of a revolution over the last five to ten years. At one time thought to be a consumer-oriented technology, AM has now evolved into a viable industrial manufacturing solution.
As of 2019, the additive manufacturing industry is estimated to be worth over $9billion dollars. While this is still a fraction of the wider $12 trillion manufacturing industry, the landscape is evolving rapidly, creating massive opportunities for the industry as a whole.
As new players continue to enter the market and new technologies are developed, now is an exciting time to be a part of the change.
With these constant shifts in the market landscape, it can be difficult for manufacturers to keep track of the key companies offering solutions across the spectrum of AM.
HAWIDO bundles all it activities around additive manufacturing under one the top additive manufacturers in india. 3D post processing technology offers equipment, process technologies and consumables for the automated post processing and surface finishing of 3D printed components, be it for single piece manufacturing or volume production. The services also include consultation regarding the optimization of component designs for the actual printing operation but also for all post processing stages. HAWIDO– Manufacturing service partner offers a comprehensive service package that includes the design/engineering of new and re-design of existing products, the printing of metallic and plastic components as well as machining and surface finishing, all focused on the field of additive manufacturing.
Design Engineers have always produced their designs based on achieving quality while utilizing the most economical methods of manufacturing. We’ve designed products to be produced by CNC machines, castings, injection molding, etc.
Additive Manufacturing (3D Printing) processes enable us to design with different boundaries and constraints. Design Engineers can incorporate geometric configurations for lightweighting, required strength, while eliminating time-consuming subtractive operations (such as EDM and CNC), conformal thermal dynamics, part-count reduction, and so much more.
Sheet Metal
Sheet metal fabrication is a subtractive manufacturing process that forms parts from thin metal sheets. Engineers often choose sheet metal parts for their high precision and durability, especially for end-use applications like chassis, enclosures, and brackets.
HAWIDOs sheet metal forming services provide a fast and cost-effective solution for any parts that need to be made from 3D CAD files or engineering drawings. We offer a range of sheet metal materials, including aluminum, copper, steel, and stainless steel. With a network of domestic and overseas fabricators, we can supply any quantity of parts from low-volume, high-mix prototypes to high-volume production runs. We offer competitive sheet metal prices for low volume prototypes and cost savings for high volume production runs.
How HAWIDO Sheet Metal Fabrication Works
HAWIDO’s metal fabrication services utilize the top sheet metal fabricators in the INDIA. Sheet metal fabricators first convert CAD and drawing data into machine code. A laser cutting, waterjet, or plasma cutting machine will then precisely remove sheet metal material. The raw material is formed into angular bends and features using brakes, punches, and dies. If any assembly or post-processing is required, our sheet metal manufacturers will weld, add inserts, or finish the part.
The efficiency and high precision of metal fabrication, coupled with HAWIDO’s variety of materials, range of sheet metal fabricators, and post-processing options means you can get parts for any application. Sheet metal applications include aerospace, defense, automotive, energy, industrial, medical, dental, and consumer products.
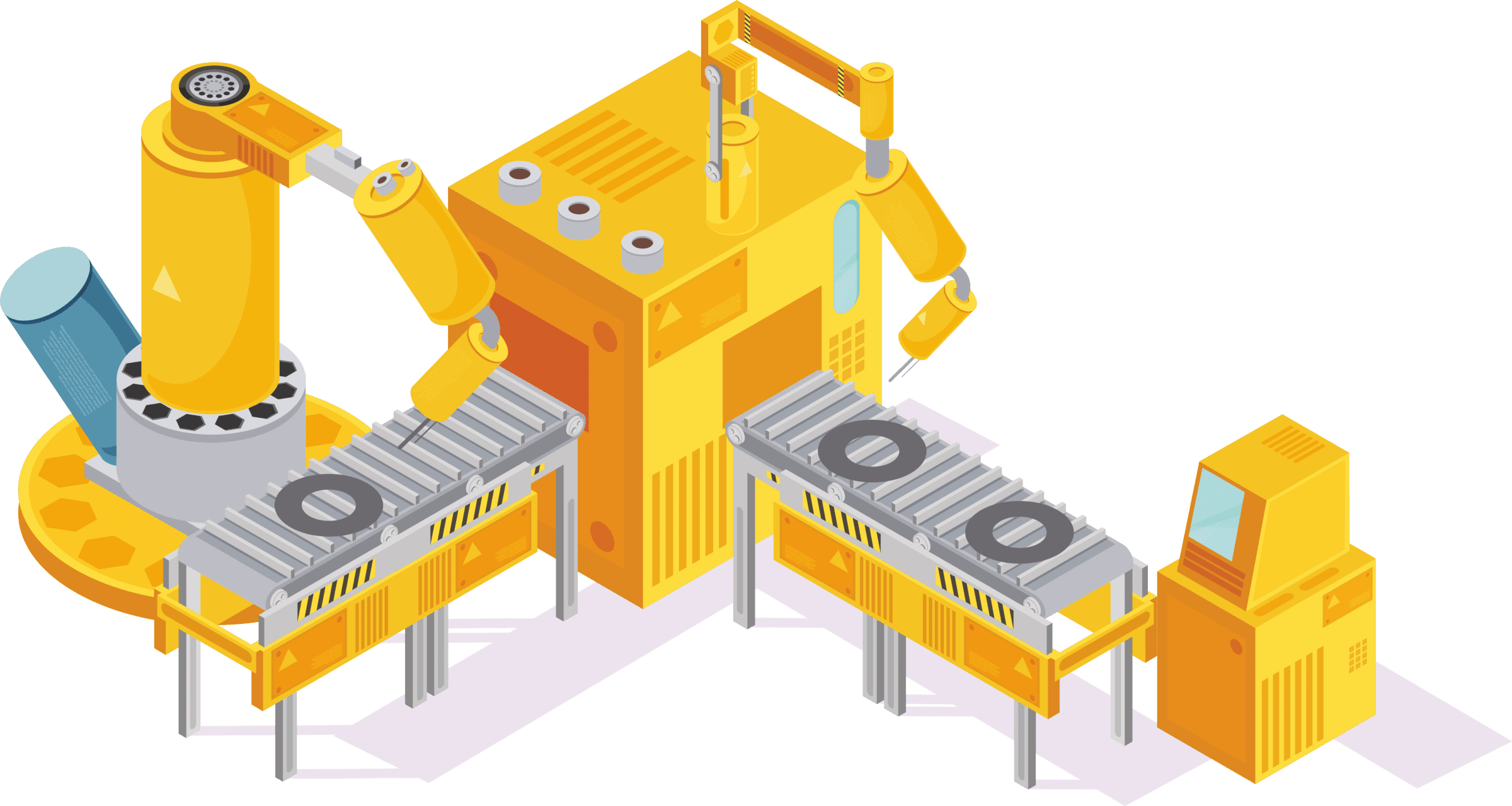
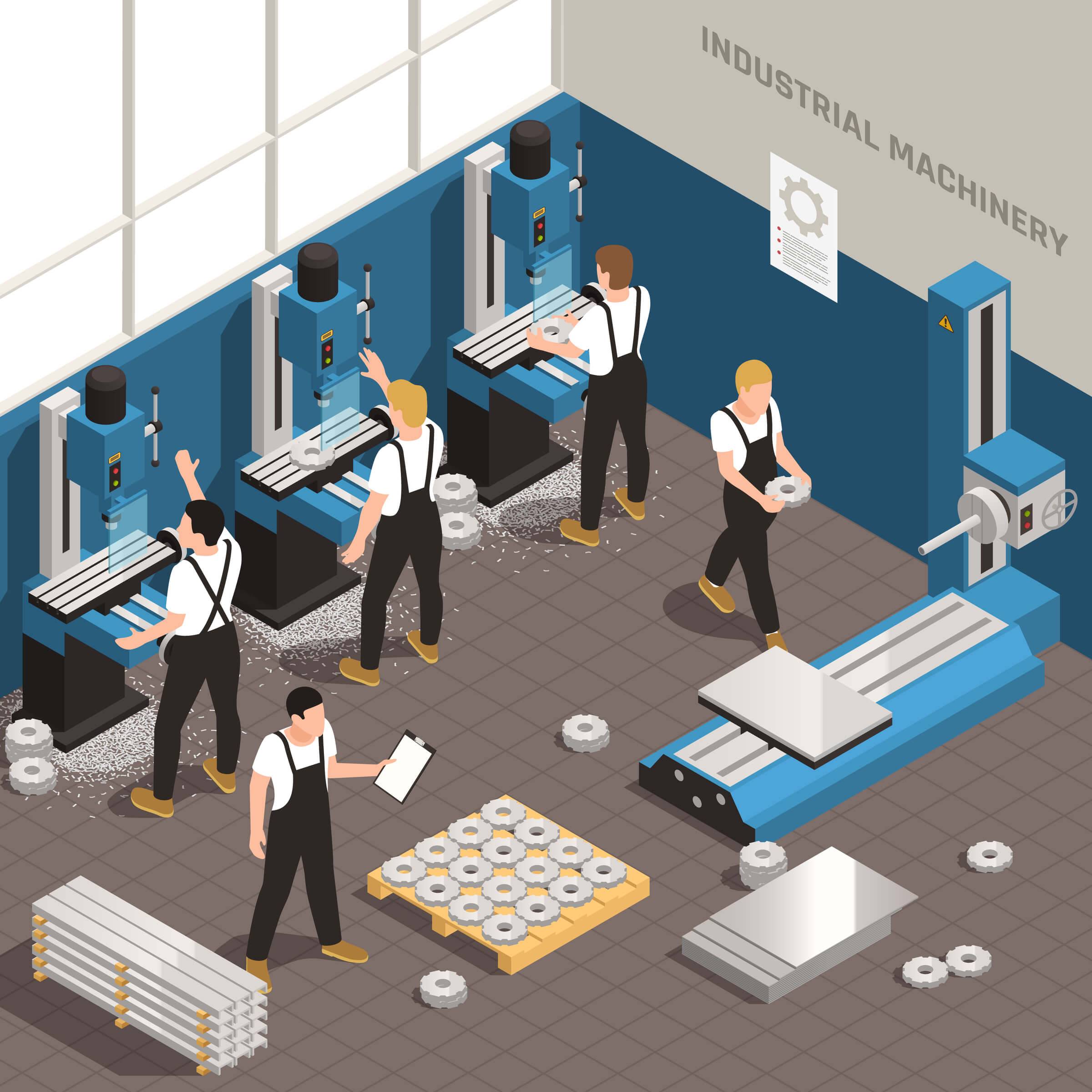
CNC Machining
CNC machining is a metal fabrication method where written code controls the machinery in the manufacturing process. The abbreviation CNC stands for computer numerical control.
Contemporary CNC machines are fully automated, eliminating the need for a manual operator to directly control the CNC machine. The code determines everything from the movement of the cutting head and the part to spindle speed and RPMs. All they need is digital files with instructions about cutting trajectories and tooling.
The part’s shape and mechanical properties are defined in a CAD file. This information is then turned into manufacturing directives for CAM (computer aided manufacturing) software. Lastly, it is transformed into specific commands for a particular machine and loaded onto the CNC machine.
Although the majority of machining processes in the manufacturing industry are controlled by computers, then in a traditional sense CNC machining refers to only a few of these automated processes, namely milling, turning and drilling.
CNC machining is a subtractive manufacturing method. This means that material gets removed during the production process, making it the opposite of additive manufacturing, e.g. 3D printing.
The benefits of CNC machines include great positioning accuracy and high repeatability, so you get consistent results every time. CNC machining is suitable for both rapid prototyping and high-volume serial production.
Plastic Injection Molding Services
We have a world-class provider of advanced plastic injection molding services. We offer a complete manufacturing solution that covers every aspect of raw material verification, tool making, part fabrication, finishing, and final inspection. Our team of manufacturing experts is committed to providing you with the highest level of professional support for plastic injection molding services of any size or complexity.
Looking for a partner to take your company’s design, manufacturing, and distribution to the next level? HAWIDO’s Injection Molding is a full-service custom plastic injection molding facility. Our goal is to be your partner. We make it possible to design, manufacture, store and distribute products in the USA at prices that are internationally competitive. As a result, with plants and distribution centers across the country, we can take your concept from sketch to reality and put it into your customers’ hands.
Whether your product is still just a concept, an improvement on an existing product or part, or it is currently being produced but you are working with multiple vendors from design to distribution, we are here to streamline the process for you.
From design to delivery, HAWIDO can help make your next big idea a reality. Our in-house team of technical designers and engineers can design, provide prototype parts, build molds and run production. We can begin immediate production on parts with your existing tooling or turn your concept into a real product. We offer bulk distribution and individual order fulfillment. With three warehouses across the US, your products are shipped efficiently and affordably.
HAWIDO builds a diverse assortment of molds, from small, single-cavity prototypes to 64-cavity, high-production molds. Our experience allows us to create molds for a variety of materials used by our customers, such as ASA, ABS, PVC, Polyethylene, and Polycarbonate.
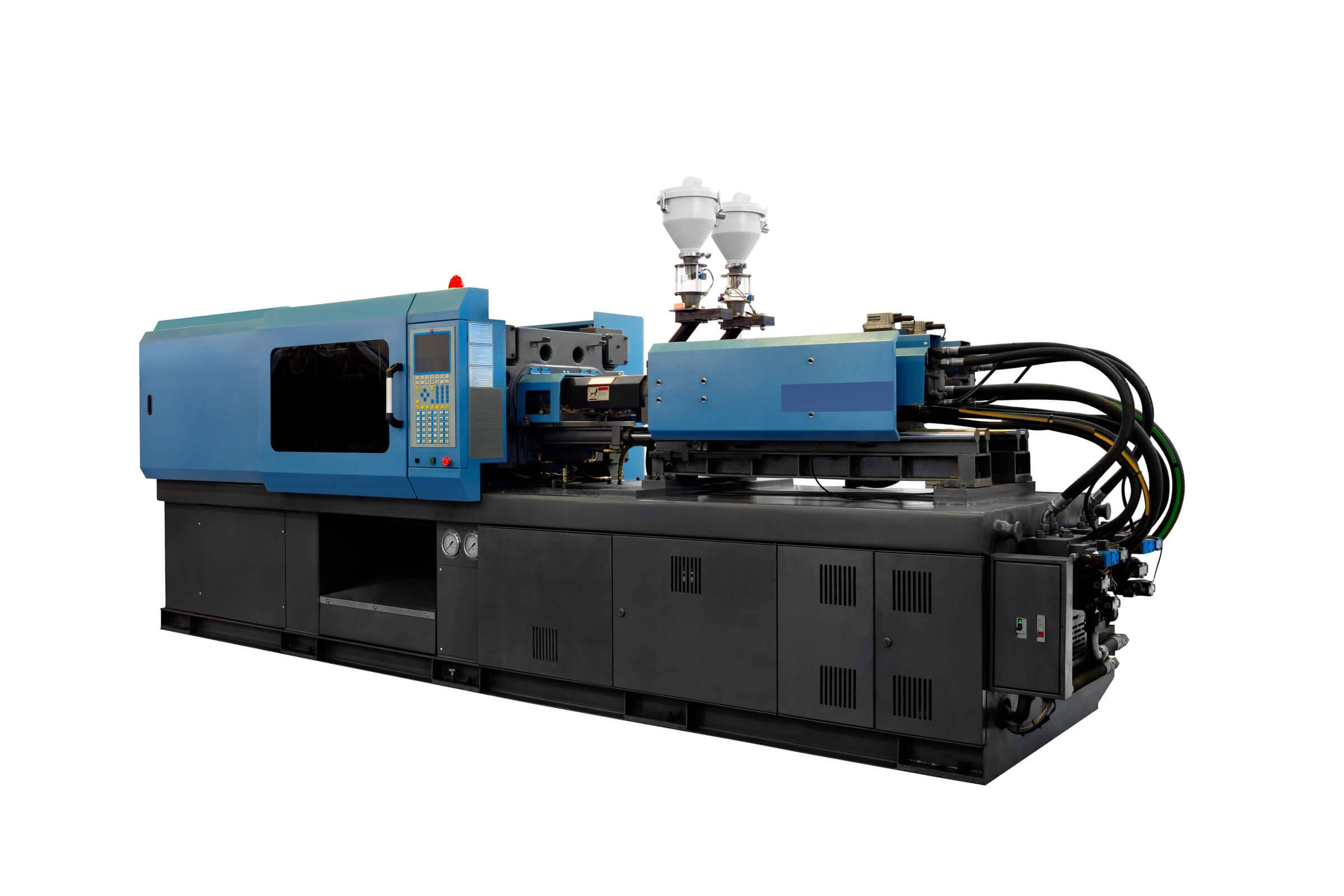
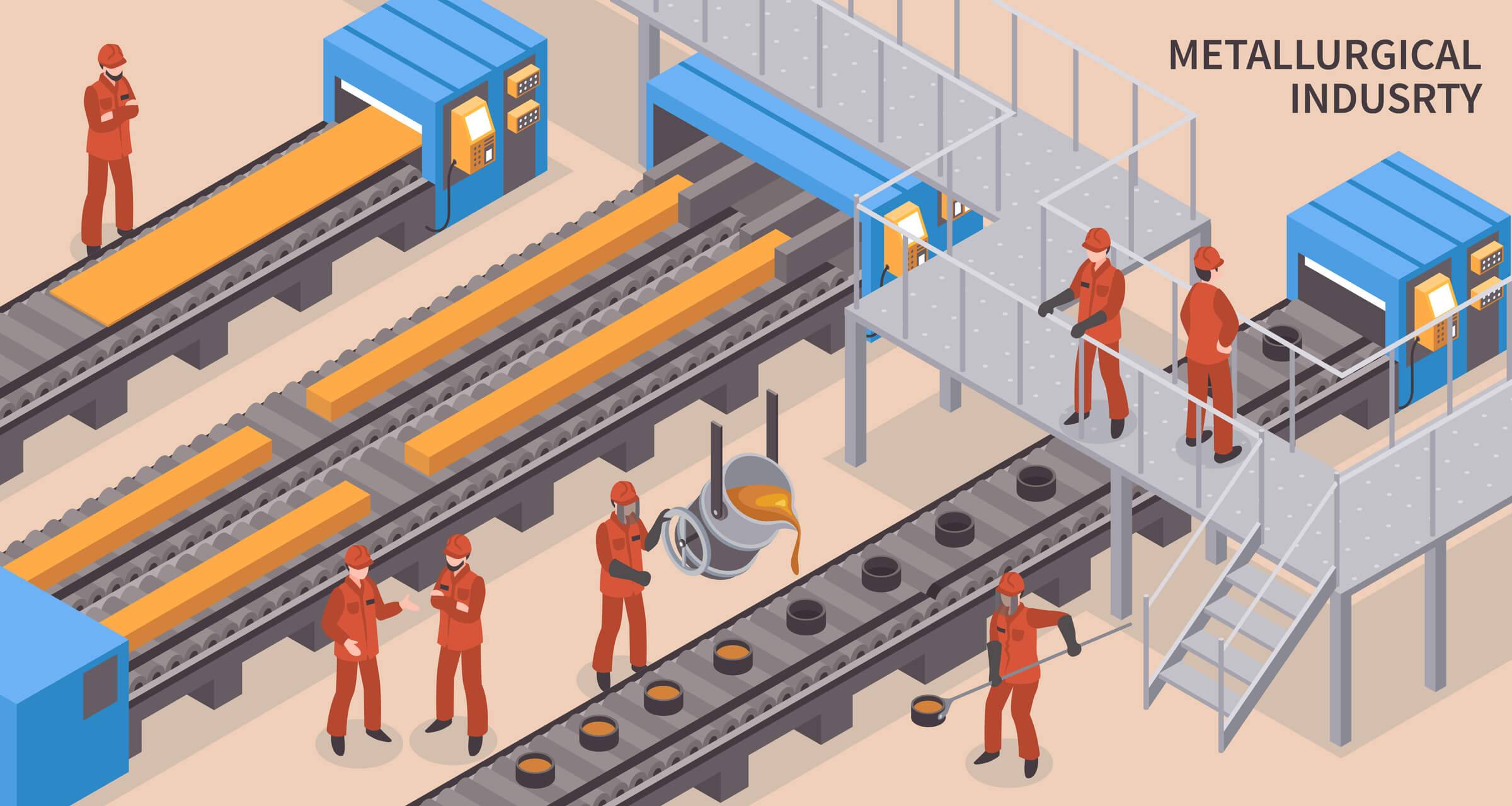
Aluminum Extrusion
Extrusion is defined as the process of shaping material, such as aluminum, by forcing it to flow through a shaped opening in a die. Extruded material emerges as an elongated piece with the same profile as the die opening.
To aid in understanding the aluminum extrusion process think about a Play-Doh Fun Factory and how it works. Think of the Fun Factory as the extrusion press, the handle as the ram, the shape bar as the die, and the Play-Doh® as the aluminum billet. The first step is to choose the desired shape and color. Think of the shape as the die and the color as the temper and alloy needed. Next, the Play-Doh® is inserted into the holding chamber and pressure is applied to the handle, which forces Play-Doh® through the shape. In an extrusion press, pressure is applied to the billet by the ram where the dummy block is attached to the end of the ram stem. When Play-Doh® begins to emerge, it has effectively been “extruded”. The same principles apply to extrusions from aluminum billets but considerably more detailed and sophisticated technologies are involved.
Press size determines how large of an extrusion can be produced. Extrusion size is measured by its longest cross-sectional dimension, i.e. its fit within a circumscribing circle. A circumscribed circle is the smallest circle that will completely enclose the cross section of an extruded shape.
The most important factor to remember in the extrusion process is temperature. Temperature is most critical because it gives aluminum its desired characteristics such as hardness and finish.
In order to help us understand your needs and requirements and service you better, the following is a checklist of things to consider when submitting items to an extruder for quoting or new business:
- Description or drawings of the part- talk to us early before the design is finalized.
- Specifications to be met; Federal specs, military, ASTM, etc.
- Alloy and temper; if unknown, indicate requirements for strength, corrosion resistance, machinability, finish, weldability, to aid the extruder in making a recommendation.
- End use length and purchase length.
- Tolerances; commercial, per drawing, other.
- Surface Finish; mill, anodize, paint, exposed surfaces, etc.
- Packaging; acceptable maximum and minimum weight per package and shipping and handling requirements.
- Secondary fabrication requirements-mitering, punching, bending, anodizing, drilling, etc.
- Product end-use.
- Quantity needed; this order and on an annual basis.
- Shipping date.
- Special quality considerations.
Plastic Extrusion
Plastic extrusion is defined as a manufacturing process (high-volume), in which the raw plastic / raw plastic material is melted and then formed in a continuous profile. With this process various products can be manufactured such as pipe/tubing, window frames, weather stripping, wire insulation, and adhesive tape. In general, the plastic materials that are used in the process of extrusion are Polyethylene, Polypropylene, Nylon (Polyamides), Polystyrene, Polycarbonate, Acetal, Acrylic, and Acrylonitrile Butadiene Styrene (ABS). These are just the primary plastic materials that are extruded. Apart from these, there are many other plastic materials that can be / are extruded all around.
Yes, we do custom profiles.
Are you in search of premium quality made plastic extrusions? HAWIDO is your one stop source for customisable solutions. We deliver step-by-step solutions to ensure you easily achieve the desired end result. Our team will be there from the initial concept all the way through to product delivery to offer unparalleled service, superior quality, and unbeatable results. With products for a wide range of applications and industries, HAWIDO is here to assist in the creation of custom solutions for the unique demands of your business.

Office No.4, Varsani House, Near Punjab National Bank, Naranpar, Bhuj Kutch 370430 Gujarat
+91 8928767596
Products
Trickle Vents
Door Levers
Corner Keys
DIDA Euro Cylinders
Window Handles
3D Hinge
Long Pull bar
Services
Pre-Productions
Productions
Corner Keys
Company
About Us
Contact Us
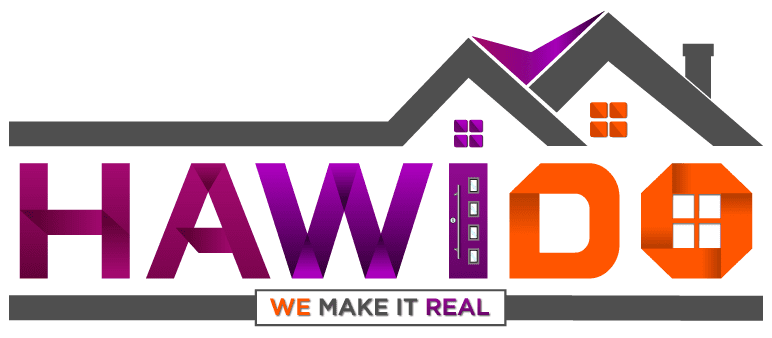
Corner Keys
Hawido is a team of engineers who research and design innovative products with customized requirements to be manufactured and Shipped to the Destination.